Rob Wilson | Principal Consultant, Greater Nashville Area | Southeast US | Connect with Rob on LinkedIn
If you have been getting mixed signals about what Digital Transformation really means, you are not alone. According to one virtual presentation I recently attended, if I were to lift my applications and data off my on-premises servers and shift them to the cloud, the rest is gravy. The only other major consideration, according to the presenter, would be to boost the throughput of my network by increasing my bandwidth. In his defense, a Cloud Strategy may indeed be a component of Digital Transformation, but that strategy is not the complete picture. It stands to reason if I have a business process that was not designed to withstand disruption, simply hosting it on someone else’s server won’t fix it. I need to take a holistic look at the process.
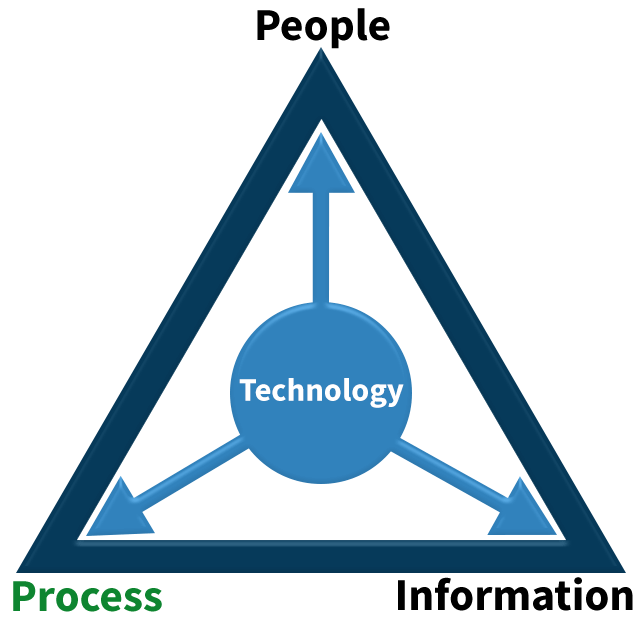
We define Digital Transformation as “the commitment of an organization to consistently improve business performance through the use of technology as a strategic asset.” The pillars of any organization are its people, processes, and information. Digital Transformation is a means to increase the effectiveness and performance of those pillars. The problem is that many organizations don’t have a solid command of their processes, and quite frankly, you cannot automate a moving target.
I once worked on a Digital Transformation initiative for a global manufacturer. The requirement was to standardize and streamline the scrap process across all departments at all plants for made-to-order (custom) finished goods. When a component was damaged, the process would be to:
- Set the assembly aside to avoid slowing the production of the following assemblies.
- Dispatch a message to the appropriate manufacturing station to produce a replacement for the damaged component and route the component ASAP to the originating assembly area.
- Get the assembly back on the line quickly so it could maintain its place in the packing queue without causing a shipping delay.
- Record the damaged component as scrapped so it could be accounted for financially and disposed of properly.
When we interviewed the plant managers, they all noted this was a glaring gap in the Enterprise Resource Planning (ERP) software. Some of them worked around it with Excel spreadsheets, Access databases, and emails. Most of them used paper, clipboards, and people running handwritten tickets from one location to another. Different departments at the same plants managed the process differently, adding to the confusion. Dozens of shipments were being delayed and thousands of dollars in scrapped items weren’t being recorded in the ledger. This was clearly a process where technology could help, but first, the plant managers had to agree upon a process that would work for each department in every plant so we could automate it.
The project was wildly successful. Manually handling tickets was replaced by printers that printed color-coded tags at the manufacturing stations to indicate a replacement component was needed right away. Workers no longer had to put down their power tools to check their email in the middle of a job. Escalation alerts were automated for assemblies that were set aside too long which risked a delayed shipment. The data was centralized, giving management full visibility of production times, quality, and the cost of scrap. Trending reports allowed them to identify problematic assembly areas and remediate them quickly. The initiative resulted in fewer backorders, a reduction in the average order-to-shipping time, a reduction in scrap costs, and a reduction in labor costs associated with manual interventions and rekeying. At the scale this company produces products, this initiative saved tens of millions of dollars annually.
In this case, the company benefited greatly from digitization, automation, integration, metricization, and standardization – some of our tenets of Digital Transformation (see our Digital Transformation Framework). It all started with clarity. When the plant managers collaborated, they realized none of them fully understood how the other plants managed damaged components and scrap. Some of them didn’t even know how certain of their own departments managed it. Eliminating ambiguity in the process design by embracing clarity was the vital first step on the path to Digital Transformation. Focus first on clarifying the process, then introduce technology to improve performance.
Think digital. Embrace clarity. Increase advantage.
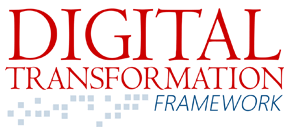
Keller Schroeder’s Digital Transformation Framework includes tenets to help you identify, prioritize, execute, and learn from transformational initiatives to better prepare you for the next disruption – whatever it may be! Click here to download your complimentary copy.